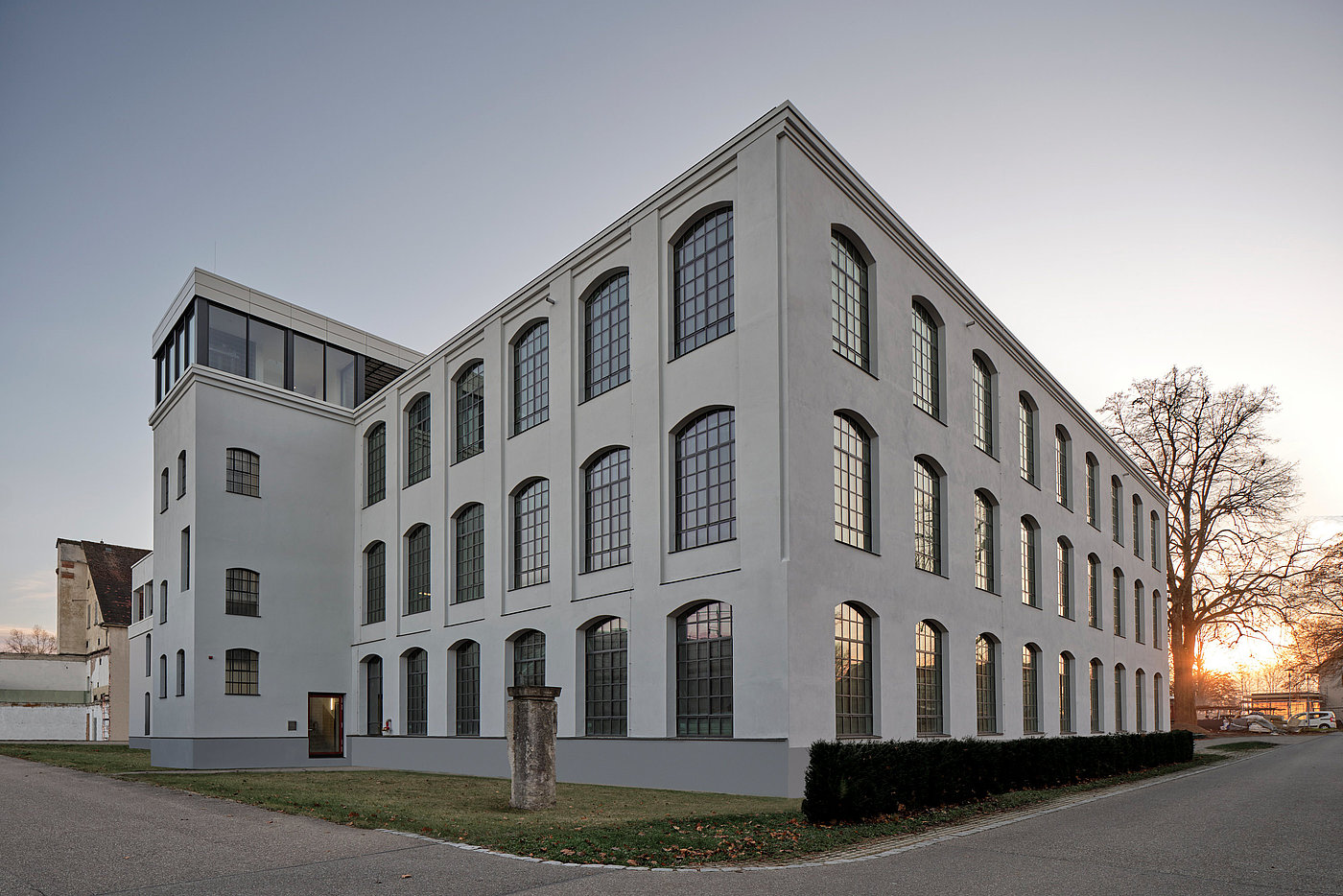
Living and working in an industrial monument
The Erlangen-Bamberg cotton spinning mill, or ERBA for short, supported numerous production facilities in southern Germany – one of them is the “Neue Spinnerei” (“new spinning mill”) in Wangen. In view of the 2024 state horticultural show, the monument has been renovated and repurposed in recent years. Thanks to the reconstruction of the large-scale industrial glazing with the Janisol Arte 66 window system, it was possible to preserve the building’s distinctive character – yet it still meets today’s energy requirements, without which converting it into a residential and commercial building would be inconceivable.
The listed “Neue Spinnerei” is located on the former ERBA site in the west side of Wangen in the Allgäu region. The building is part of the “Baumwoll-spinnerei Wangen” (“Wangen cotton spinning mill”) cultural monument; its refurbishment and conversion into a residential and commercial building will take place in parallel with the revitalisation of the entire factory premises in the run-up to the 2024 state horticultural show. However, the “new” does not refer to the current refurbishment and repair work, but to two buildings from 1900 and 1908, respectively, which expanded the “Alte Spinnerei” (“old spinning mill”) at the time. The “Neue Spinnerei” consists of a two-storey south-facing building from 1900, the adjacent three-storey north-facing building from 1908 and an additional storey from 1957 with which the height of the south-facing building was aligned with the north-facing building. There are only a few years between the building of 1900 and that of 1908, and yet the difference between the two is a quantum leap from an architectural point of view: While the construction dating back 1900 was adapted to the design of the “Alte Spinnerei,” Philipp Jakob Manz, one of the leading industrial architects of his time, introduced a contemporary architectural language to the site with the extension in 1908. This is expressed in the almost full-surface glazing of the facades. This was made possible by the steel frame construction, which was still modern at the time: Not only did it noticeably shorten construction times (which earned Manz the reputation of being a “lightning architect”), but it also made possible the extremely large facade openings, which greatly increased the amount of daylight in the spinning halls.
Project details
Windows
2020
- Architecture
Grath Architekten, Ravensburg/DE
- Metal construction
Forster Fassadentechnik GmbH, Mitterteich/DE
- Schüco aluminium systems
ASS 70.HI